In the context of robotics, accurate ground-truth positioning is the cornerstone for the development of mapping and localization algorithms. In outdoor environments and over long distances, RTSs (Robotic Total Station) provide accurate and precise measurements, that are unaffected by the usual factors that deteriorate the accuracy of Global Navigation Satellite System (GNSS). In this project, we focus on the unexplored problem of having the six DOF (Degrees Of Freedom) of a mobile robotic platform with three RTSs, each of them tracking dynamically one different prism.
The main goal of this project is to extend the current use of RTS in robotics to obtain accurate and precise ground-truth in different type of environment. Research done in this field use already either three static prisms to obtain the six DOF of a platform with one RTS, either one RTS tracking dynamically one prism to obtain its position, i.e. its three DOF. We want to push forward these knowledge by developping a system which can obtain the six DOF of a robot with three RTS tracking dynamically three prisms. This project is adressing also the processing of the RTS data. Few example are given in the robotics community and no details are available about experiments done in papers using RTS. We aim to improve the accuracy and precision of the ground-truth by pre-processing the data gathered by our system.
To achieve the goals of the project, the following specific objectives are defined:
- Objective 1—System design and functionality: to develop the system of three RTSs tracking three different prisms and compare its precision to GNSS.
- Objective 2—Highly precise extrinsic calibration: to develop an algorithm to do an extrinsic calibration of our system based on the dynamic tracking of three prisms.
- Objective 3—Uncertainty and metric evaluation: to carry out an extensive series of experiments using our system of three RTSs to have several ground-truth and evaluate our mapping algorithms.
Publications
- Vaidis, M., Dubois, W., Daum, E., LaRocque, D., & Pomerleau, F. (2023). Uncertainty analysis for accurate reference trajectories with robotic total stations. Proceedings of the IEEE International Conference on Intelligent Robots and Systems (IROS). https://ieeexplore.ieee.org/abstract/document/10341529 Accepted for oral presentation
Publisher Bibtex source - Vaidis, M., Dubois, W., Guénette, A., Laconte, J., Kubelka, V., & Pomerleau, F. (2023). Extrinsic calibration for highly accurate trajectories reconstruction. Proceedings of the IEEE International Conference on Robotics and Automation (ICRA). https://arxiv.org/abs/2210.01048
Publisher Bibtex source - Vaidis, M., Giguère, P., Pomerleau, F., & Kubelka, V. (2021). Accurate outdoor ground truth based on total stations. 2021 18th Conference on Robots and Vision (CRV). https://arxiv.org/abs/2104.14396
PDF Publisher Bibtex source
1. System design and functionality
Access to precise and accurate ground-truth pose reference during experiments is vital in mobile robotics. For instance, knowing the pose of a robot, that is its position and orientation, facilitates development and testing of localization, mapping and control algorithms. For indoor experiments, motion capture such as the Vicon or Optitrack systems have become the de facto standard. They are based on tracking reflective or active markers by infrared cameras and offer an accuracy of sub-millimetre precision and high sampling rates. However, the area that they can cover is limited by the number of cameras available. Moreover, they struggle in direct sunlight. The possibilities of pose reference are more limited outdoors. The approaches most prominent in the literature use GNSS, RTS, and qualitative comparison of trajectories to maps. Besides, these outdoor referencing systems do not provide direct orientation measurements.
When it comes to gathering datasets in forests, accuracy of Real Time Kinematics (RTK) positioning suffers from signal attenuation by vegetation. Consequently, the need for accurate and precise pose reference immune to foliage interference and signal reflection has motivated the development of a system based on multiple RTSs appropriate for such task. We propose a protocol for a novel referencing system relying on multiple RTSs to allow the measurement of the six DOF of a vehicle. The setup design is shown here:
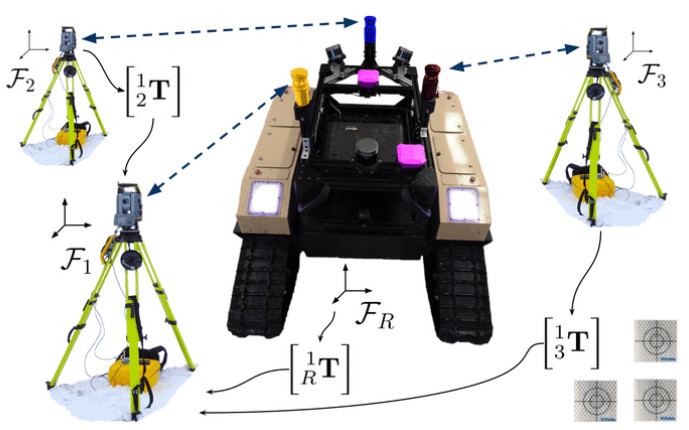
Each RTS tracks one prism dynamically and the data are collected with a Raspberry Pi setup. They send the data over a LoRa protocol to a Raspberry Pi master located on the robotic platform moving during an experiment. The inter-prism distances are supposed to be fixed and are used as a metric to quantify the uncertainty of the measurements. The data gathered are all expressed in the same frame through an extrinsic calibration. More details about the setup are available Here.
2. Highly precise extrinsic calibration
The use of multiple RTSs to obtain the six DOF of a robotic platform requires two necessary conditions: 1) All data must be expressed in a common coordinate frame based on an extrinsic calibration, also called resection or free-stationing in the surveying field. In the literature, there are several extrinsic calibration methods for multiple RTSs based on static Ground Control Points (GCPs). Yet, they require a significant effort in preparation and special equipment such as geodesic pillars to achieve the desired accuracy. 2) the RTS measurements need to be synchronized. Contrary to position measurements from GNSS receivers, the measurements are not executed synchronously between multiple RTSs by default since this functionality is usually not required in surveying. Therefore, temporal interpolation is necessary to exploit the data from these different RTSs to obtain the robotic platform’s pose.
We propose an extrinsic calibration method for three RTSs while a vehicle is in motion (i.e., without having to set up static reference points in the environment). This method does not require manual registration of additional reference points, and the same configuration is used both for the calibration and the subsequent ground truth positioning, drastically reducing the setup time. The method exploits the known distances between the prisms attached to the robotic platform and only requires the robot to be driven along a random trajectory throughout the experimental area.
The following video shows a summary of our issue and the solution we provided:
We evaluate the proposed approach against existing extrinsic calibration methods for RTS using a dataset consisting of more than 30 km of indoor and outdoor trajectories. These datasets and the code are available online to the community at Github Project RTS. The paper is available Here.
3. Uncertainty and metric evaluation (work in progress)
Having our system and a precise way to obtain the data, we can now focus on generating precise ground-truth for multiple user cases. Ground-truth can already be generated with this RTS system. We are still working on some improvments to take into account the uncertainty of the measurement, and we will evaluate different metrics to compare both ground-truth and mapping computed by our mapping algorithm.
Here is an example of a comparison between our ground-truth taken with our setup and an ICP result:
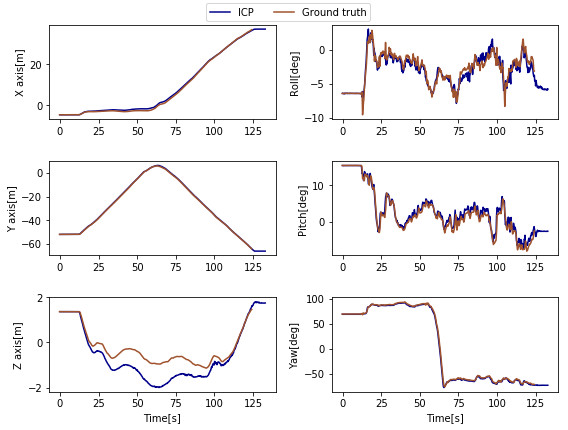
4. Lessons learned
Good levelling
The levelling of the RTS is very important to obtain accurate measurements. Most of the experiments can be done on solid surface such as asphalt. However, in forest enviromnent we had to struggle to obtain a correct levelling, especially during winter times. We found out the levelling is easier when we removed all the snow under the RTS and set them directly on the frozen ground as shown in this picture:
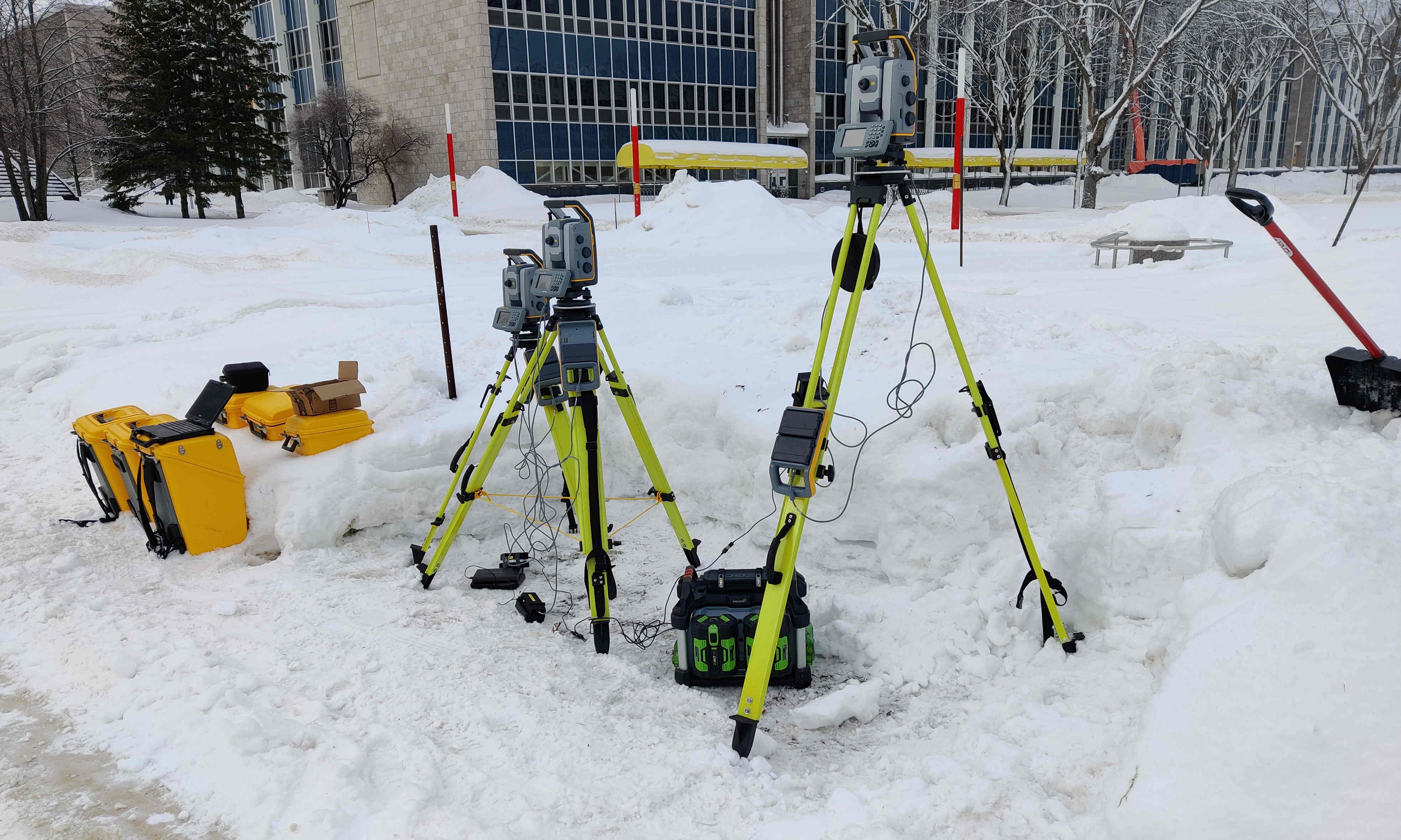
If it’s not possible, we suggest to pack the snow around the tripods of the RTS.
Vibration issue for top prism
Prisms located on the robotic platform are set with different height so the RTSs can tracked them easily. Because of this setup, the top prism can be subject to high vibrations as shown in this video:
To fix this issue, we added more fixations to reduce the vibrations:
Sensor extrinsic calibration
To obtain the inter-prism distances of one deployment, we do the sensors extrinsic calibration quiclky after the end of the deployment. Because of vibration in the system during experiments, a too long wait between two deployments can lead to an error of 2 to 5mm in these distances. Therefore, we do the extrinsic calibration rigth after one deployment. The process can take between 15 to 45min depending of the number of markers to get. This extrinsic calibration is done with one RTS, and we do it with the main sensors one the robotic plateform, i.e. prisms, lidar and GPS, as shown in this picture:
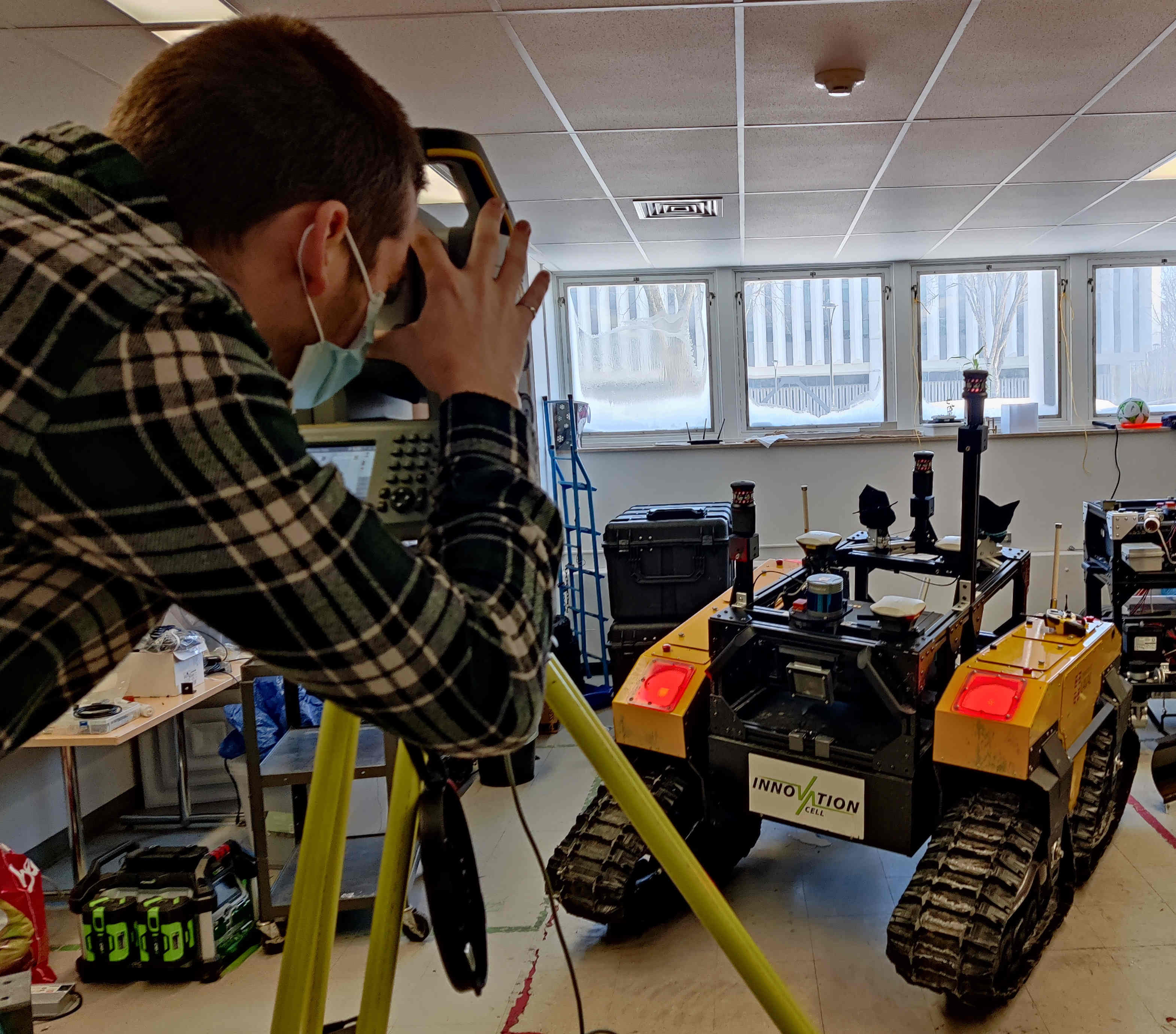
We tilt the robotic platform to an angle of more than 20 degrees to reduce the uncertainty of the measurements gathered by the RTS. A too flat surface leads to an lower precision due to the reflective markers used. For the same reason, we use the maximum height of the RTS to increase the incidence angle between the reflective marker and the RTS. Each mesurement kept is the average of 10 measurements.
Tips for deployments
- Temperature: Place the equipment in the deployment area at least 40 minutes before uing them.
- RTSs height: RTSs are set at a different height on the ground to have fewer occlusions during a deployment
- Prisms height: Prisms are set at a different height on robotic platform to have fewer occlusions during a deployment
- Communication range: Raspberry Pi with the LoRa module should be high to have a longer communication range. We can aim to have a kilometer range with our setup in an open field.
Team
- Principal Investigator and Technical Lead: François Pomerleau
- Deputy Technical Lead: Vladimír Kubelka
- Postdoc: Johann Laconte
- PhD student: Maxime Vaidis
- Master student: William Dubois
- Trainee: Alexandre Guénette